Samarium Cobalt magnets: good thermal stability, resistant to corrosion, resistant to demagnetization
A samarium-cobalt (SmCo) magnet, a type of rare earth magnet, is a strong permanent magnet made of an alloy of samarium and cobalt.
They are generally ranked similarly in strength to neodymium magnets, but have higher temperature ratings and higher coercivity.
samarium-cobalt (SmCo) magnets are brittle, and prone to cracking and chipping. Samarium-cobalt magnets have maximum energy products (BHmax) that range from 16 megagauss-oersteds (MGOe) to 33 MGOe, approx. 128 kJ/m3 to 264 kJ/m3; their theoretical limit is 34 MGOe, about 272 kJ/m3.
samarium-cobalt (SmCo) magnets are available in two "series", namely Series 1:5 and Series 2:17.
Sintered Samarium Cobalt magnets exhibit magnetic anisotropy, meaning they can only be magnetized in the axis of their magnetic orientation. This is done by aligning the crystal structure of the material during the manufacturing process.
Machining & Magnetization
Samarium Cobalt magnets offer strong resistance to demagnetization. All Samarium Cobalt magnets cannot be formed with conventional drilling, turning or milling processes, and must be ground before they are magnetized. Additionally, large or complex assemblies are usually magnetized prior to assembly. Standard tolerances for Samarium Cobalt magnets are +/-.005 for ground dimensions.
1:5 alloy material
1:5 offers 16 MGOe (energy product) to 22 MGOe and is made up of approximately 50% samarium and 50% cobalt. The 1:5 series has a maximum recommended operating temperature of 250°C. SmCo 1:5 magnets require lower field strengths than 2:17 materials to magnetize. In some instances, 1:5 material may be magnetized with multiple poles, provided that a magnetizing fixture is available.
2:17 alloy material
2:17 offers 24 MGOe to 32 MGOe and is composed of about 25% samarium, 5% copper, 18% iron, 2% hafnium or zirconium, with the remainder being cobalt. The 2:17 series has a maximum operating temperature of 350°C. Special grades of 2:17 are available which can operate to even higher temperatures. SmCo 2:17 requires a higher magnetizing field than alloy 1:5 does, and multiple pole magnetization is sometimes possible, provided that a magnetizing fixture is available.
Performance for samarium cobalt magnets:
Features include:
Samarium cobalt magnets are hard and brittle and may chip or break if dropped.
They have high magnetic properties
Samarium cobalt magnets offer good thermal stability
Samarium cobalt magnets are resistant to corrosion
Samarium cobalt magnets resistant to demagnetization
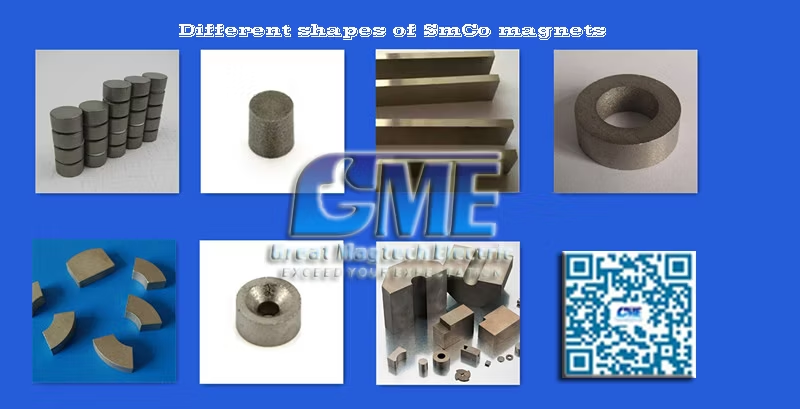
Advantages:
Manufacturing Methods
SmCo magnets are manufactured in the following forms:
Sintered - fine SmCo powder is compacted in a die and then sintered, fusing the powder into a solid material. There are two forms of pressing: die pressing (which involves a hard die into which the powder is placed and then pressed), and isostatic pressing (involving a special "rubber" die into which powder is placed and then pressed with equal force in all directions on the powder). Die pressed parts are smaller than isostatically pressed parts. Although the magnetic properties of isostatically pressed parts are higher, the uniformity of magnetic characteristics is usually lower than that of die pressed parts. Sintered parts usually need some finish machining in order to meet final tolerances.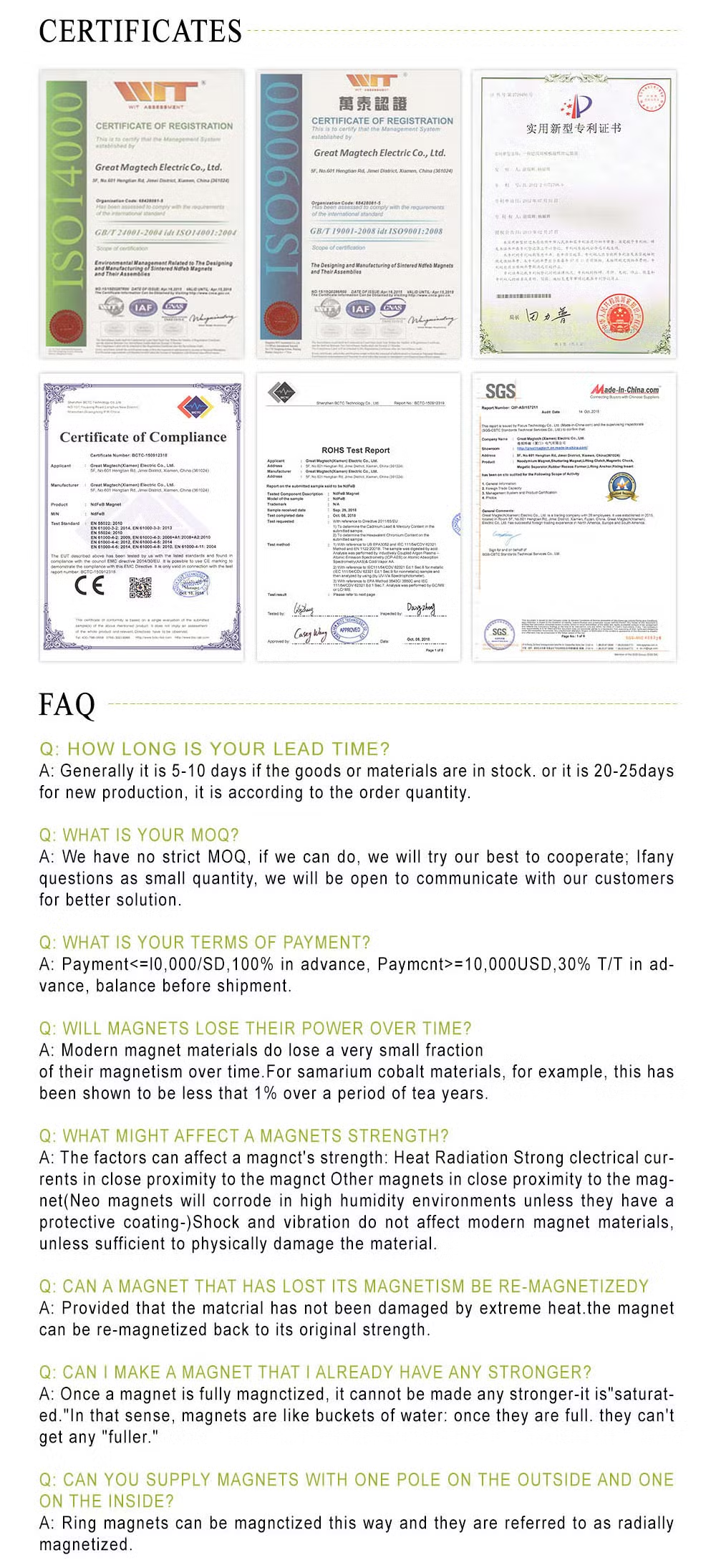
A samarium-cobalt (SmCo) magnet, a type of rare earth magnet, is a strong permanent magnet made of an alloy of samarium and cobalt.
They are generally ranked similarly in strength to neodymium magnets, but have higher temperature ratings and higher coercivity.
samarium-cobalt (SmCo) magnets are brittle, and prone to cracking and chipping. Samarium-cobalt magnets have maximum energy products (BHmax) that range from 16 megagauss-oersteds (MGOe) to 33 MGOe, approx. 128 kJ/m3 to 264 kJ/m3; their theoretical limit is 34 MGOe, about 272 kJ/m3.
samarium-cobalt (SmCo) magnets are available in two "series", namely Series 1:5 and Series 2:17.
Sintered Samarium Cobalt magnets exhibit magnetic anisotropy, meaning they can only be magnetized in the axis of their magnetic orientation. This is done by aligning the crystal structure of the material during the manufacturing process.
Machining & Magnetization
Samarium Cobalt magnets offer strong resistance to demagnetization. All Samarium Cobalt magnets cannot be formed with conventional drilling, turning or milling processes, and must be ground before they are magnetized. Additionally, large or complex assemblies are usually magnetized prior to assembly. Standard tolerances for Samarium Cobalt magnets are +/-.005 for ground dimensions.
1:5 alloy material
1:5 offers 16 MGOe (energy product) to 22 MGOe and is made up of approximately 50% samarium and 50% cobalt. The 1:5 series has a maximum recommended operating temperature of 250°C. SmCo 1:5 magnets require lower field strengths than 2:17 materials to magnetize. In some instances, 1:5 material may be magnetized with multiple poles, provided that a magnetizing fixture is available.
2:17 alloy material
2:17 offers 24 MGOe to 32 MGOe and is composed of about 25% samarium, 5% copper, 18% iron, 2% hafnium or zirconium, with the remainder being cobalt. The 2:17 series has a maximum operating temperature of 350°C. Special grades of 2:17 are available which can operate to even higher temperatures. SmCo 2:17 requires a higher magnetizing field than alloy 1:5 does, and multiple pole magnetization is sometimes possible, provided that a magnetizing fixture is available.
Performance for samarium cobalt magnets:
Material | Grade | Remannence | Coercive Force | Instrinsic Coercive | Max Energy | Density | Temp Coefficient | Temp Coefficient | Cuire Temp | Max Working Temp. (TW) | ||||
(Br) | (Hcj) | (Hcb) | (BHmax) | (D) | (Near Br) | (Near Hcj) | (TC) | |||||||
mT | Gs | KA/m | Oe | KA/n | Oe | KJ/m3 | MGOe | g/cm3 | %/K | %/K | ºC | ºC | ||
SmCo 1:5 | SmCo18 | 840 | 8400 | 605 | 7600 | 1432 | 18000 | 143 | 18 | 8.1 | -0.04 | -0.3 | 750 | 250 |
(SmPr)CO5 | SmCo20 | 890 | 8900 | 637 | 8000 | 1432 | 18000 | 159 | 20 | 8.2 | -0.04 | -0.3 | 750 | 250 |
SmCo22 | 930 | 9300 | 637 | 8000 | 1432 | 18000 | 175 | 22 | 8.2 | -0.04 | -0.3 | 750 | 250 | |
LTc(HM-10) | 590 | 630 | 493 | 6200 | 1430 | 1830 | 80 | 10 | 8.2 | Temp Range | %ºC | 700 | 250 | |
1:5 | 20-100ºC | -0.004 | ||||||||||||
(SmGd)CO5 | 100-200ºC | -0.021 | ||||||||||||
200-300ºC | -0.042 | |||||||||||||
SmCo24 | 980 | 9800 | 676 | 8500 | 1432 | 18000 | 191 | 24 | 8.3 | -0.03 | -0.2 | 800 | 280 | |
SmCo24H | 980 | 9800 | 676 | 8500 | 1989 | 25000 | 191 | 24 | 8.3 | -0.03 | -0.2 | 800 | 280 | |
SmCo26L | 1030 | 10300 | 398 | 5000 | 438 | 5500 | 207 | 26 | 8.3 | -0.03 | -0.2 | 800 | 300 | |
SmCo26 | 1030 | 10300 | 716 | 9000 | 1194 | 15000 | 207 | 26 | 8.3 | -0.03 | -0.2 | 800 | 300 | |
2:17 Sm2 | SmCo26M | 1030 | 10300 | 716 | 9000 | 1592 | 20000 | 207 | 26 | 8.3 | -0.03 | -0.2 | 800 | 300 |
(CoFeCUZr)17 | SmCo26H | 1030 | 10300 | 716 | 9000 | 1989 | 25000 | 207 | 26 | 8.3 | -0.03 | -0.2 | 800 | 350 |
SmCo28 | 1070 | 10700 | 756 | 9500 | 1194 | 15000 | 223 | 28 | 8.3 | -0.03 | -0.2 | 800 | 350 | |
SmCo28M | 1070 | 10700 | 756 | 9500 | 1592 | 20000 | 223 | 28 | 8.3 | -0.03 | -0.2 | 800 | 350 | |
SmCo30 | 1100 | 11000 | 772 | 9700 | 1194 | 15000 | 239 | 30 | 8.3 | -0.03 | -0.2 | 800 | 350 | |
SmCo30M | 1100 | 11000 | 772 | 9700 | 1592 | 20000 | 239 | 30 | 8.3 | -0.03 | -0.2 | 800 | 350 | |
LTc(HMG-22) | 980 | 9800 | 715 | 9000 | 1500 | 20000 | 230 | 23 | 8.3 | Temp Range | %ºC | 840 | 300 | |
2:17 | -50-25ºC | 0.005 | ||||||||||||
(SmEr)2(CoTM)17 | 20-100ºC | 0.012 | ||||||||||||
100-200ºC | 0.006 | |||||||||||||
200-300ºC | -0.025 |
Samarium cobalt magnets are hard and brittle and may chip or break if dropped.
They have high magnetic properties
Samarium cobalt magnets offer good thermal stability
Samarium cobalt magnets are resistant to corrosion
Samarium cobalt magnets resistant to demagnetization
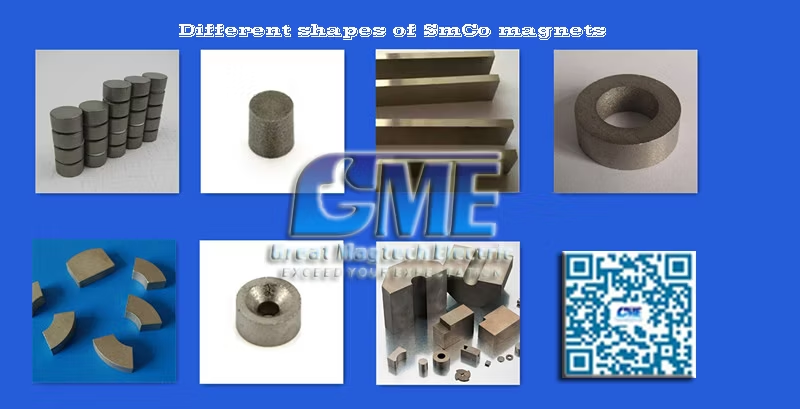
Advantages:
- Extremely resistant to demagnetization
- high temperature stability (max operating temperatures between 250 °C (523 K) and 550 °C (823 K); Curie temperatures from 700 °C (973 K) to 800 °C (1,070 K)
- Expensive and subject to price fluctuations (cobalt is market price sensitive)
- Samarium cobalt magnets can easily chip; eye protection must be worn when handling them.
- Allowing magnets to snap together can cause the magnets to shatter, which can cause a potential hazard.
- Samarium-cobalt is manufactured by a process called sintering, and as with all sintered materials, inherent cracks are very possible. These magnets do not have mechanical integrity; instead the magnet must be utilized for its magnetic functions and other mechanical systems must be designed to provide the mechanical reliability of the system.
Property | Neodymium | Sm-Co |
Remanence (T) | 1-1.3 | 0.82-1.16 |
Coercivity (MA/m) | 0.875-1.99 | 0.493-1.59 |
Relative permeability | 1.05 | 1.05 |
Temperature coefficient of remanence (%/K) | 0.12 | 0.03 |
Temperature coefficient of coercivity (%/K) | 0.55..-0.65 | 0.15..-0.30 |
Curie temperature (°C) | 320 | 800 |
Density (g/cm3) | 7.3-7.5 | 8.2-8.4 |
CTE, magnetizing direction (1/K) | 5.2×106 | 5.2×106 |
CTE, normal to magnetizing direction (1/K) | 0.8×106 | 11×106 |
Flexural strength (N/mm2) | 250 | 150 |
Compressive strength (N/mm2) | 1100 | 800 |
Tensile strength (N/mm2) | 75 | 35 |
Vickers hardness (HV) | 550-650 | 500-650 |
Electrical resistivity (Ω·cm) | (110-170)×106 | 86×106 |
SmCo magnets are manufactured in the following forms:
Sintered - fine SmCo powder is compacted in a die and then sintered, fusing the powder into a solid material. There are two forms of pressing: die pressing (which involves a hard die into which the powder is placed and then pressed), and isostatic pressing (involving a special "rubber" die into which powder is placed and then pressed with equal force in all directions on the powder). Die pressed parts are smaller than isostatically pressed parts. Although the magnetic properties of isostatically pressed parts are higher, the uniformity of magnetic characteristics is usually lower than that of die pressed parts. Sintered parts usually need some finish machining in order to meet final tolerances.
- Compression Bonded - this is a technique whereby a special form of SmCo powder is blended with a plastic carrier material, die pressed and then heated. Parts made in this way can be of complex shapes and come off the tool with close tolerances, requiring no further finish machining. They have lower energy products than sintered materials - currently in the range of 15 MGOe.
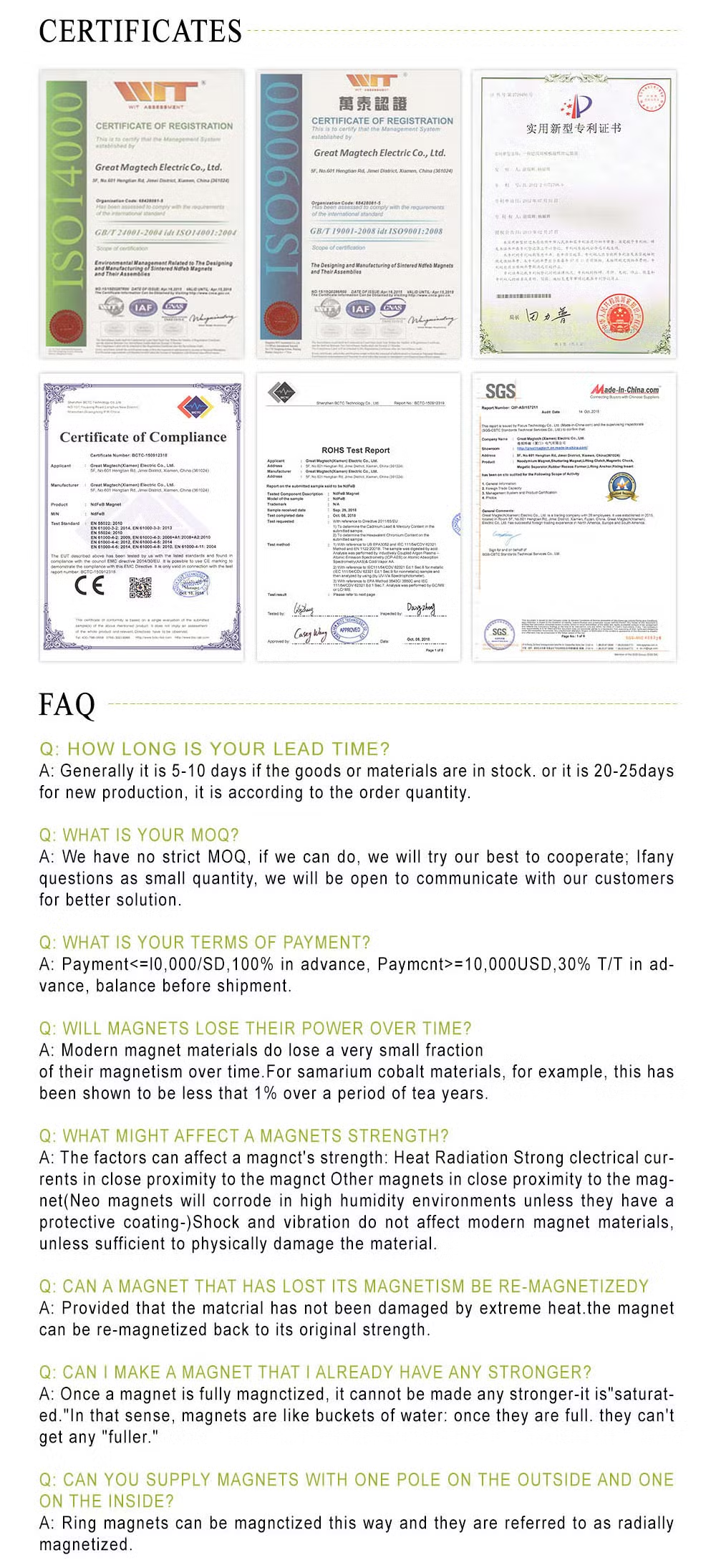